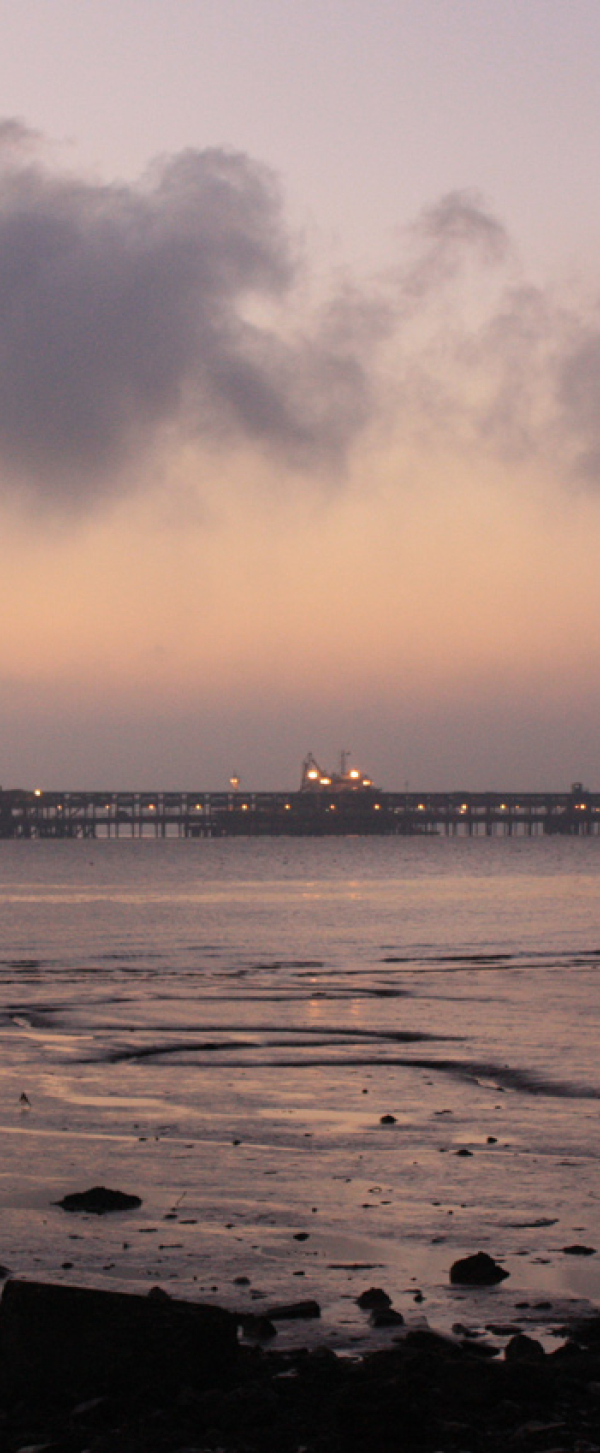
Saltend Jetty
VolkerLaser has undertaken six phases of works to the Saltend Jetty, in Hull, for client, Associated British Ports (ABP).
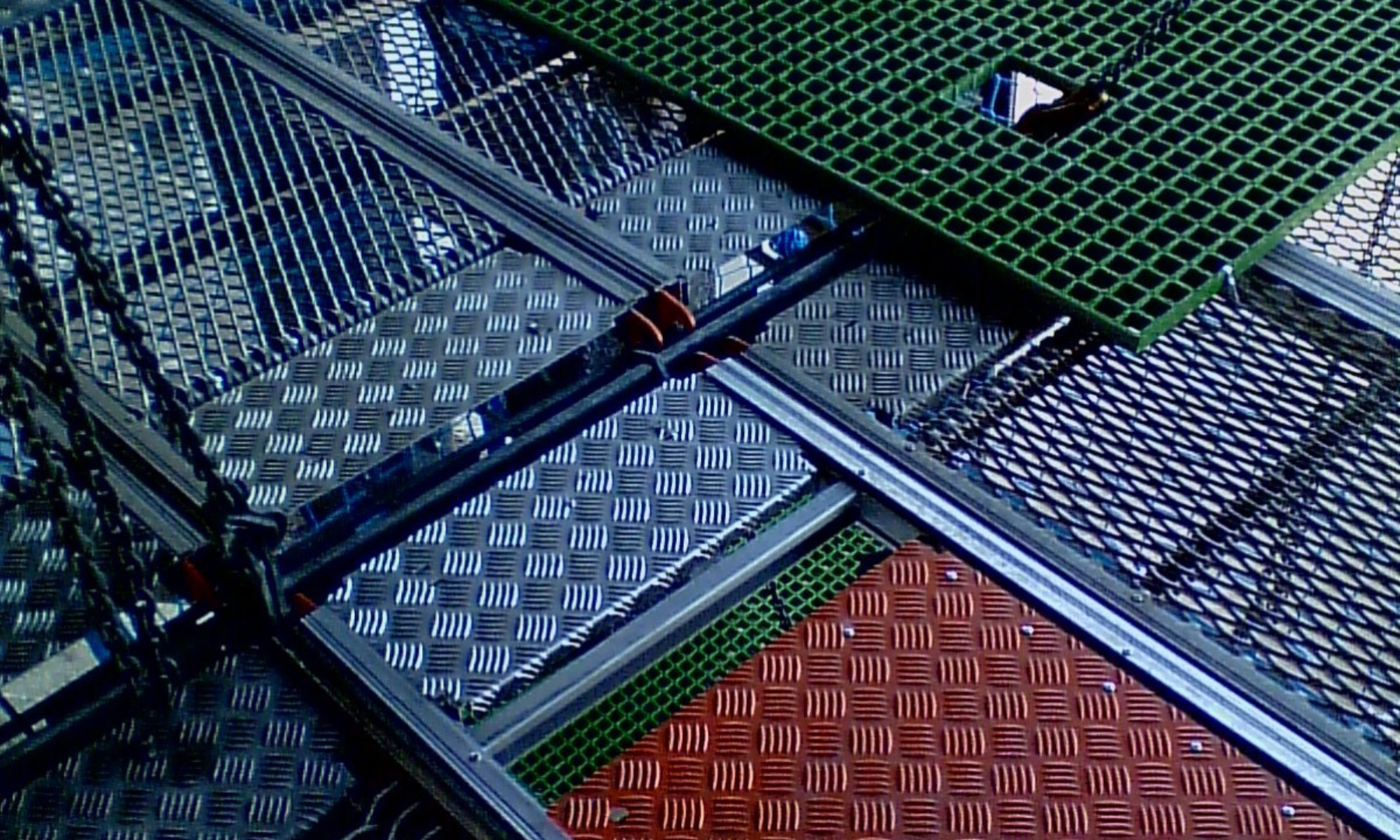
What we did
Since 2013, VolkerLaser has worked for ABP, providing repair and strengthening services to maintain the jetties which are used by large vessels to unload sensitive chemicals. The collaborative relationship, and the team’s intricate knowledge of the structures, are key to ensuring the success of the projects, as there are a number of logistical and environmental challenges to manage throughout.
In order to undertake the concrete repair works to the underside of the jetties, an accessible and safe working area needed to be created, taking into consideration the high tide, port traffic and environmental concerns. Working with ABP, during an Early Contractor Involvement (ECI) period, VolkerLaser proposed the use of the innovative under deck access system - V-Deck™.
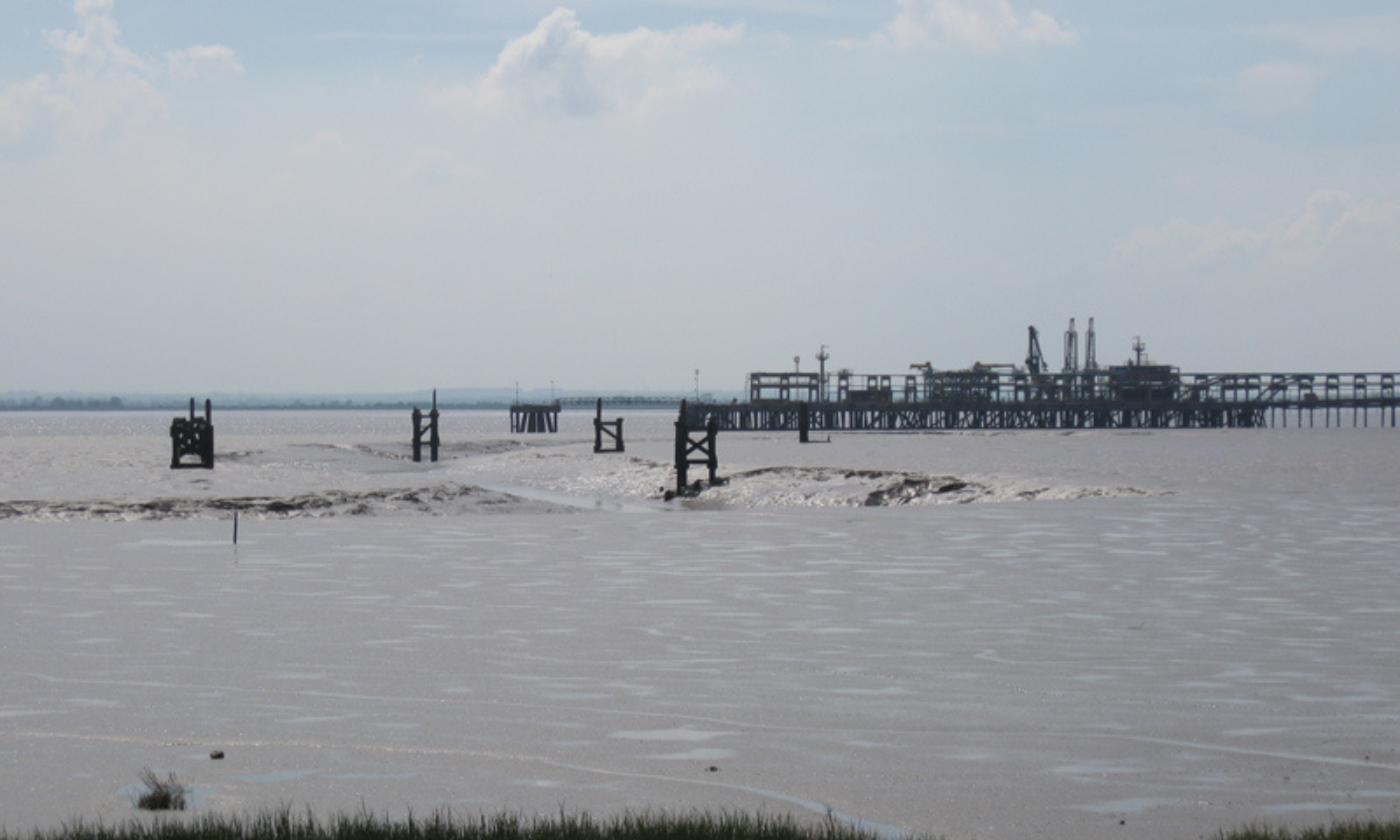
In previous phases, a scaffolding solution had been used, however, the V-Deck™ system was designed to allow submersion at high tides, whilst also considering potential wave impact. The use of V-Deck™ also meant works could continue with rope access during periods of rising or falling tides, whereas the scaffolding option would only facilitate works at low tide. These benefits, combined with a faster installation time, and a reduced safety boat requirement, meant The VolkerLaser team installed 150m² of V-Deck™ to jetty one, and 200m² to jetty three, with various encapsulation options erected, depending on the works being undertaken. Due to the Humber estuary being a Site of Special Scientific Interest (SSSI), extensive controls for dust and waste management were in place throughout the works, as well as pollution controls during the concrete breakout works.
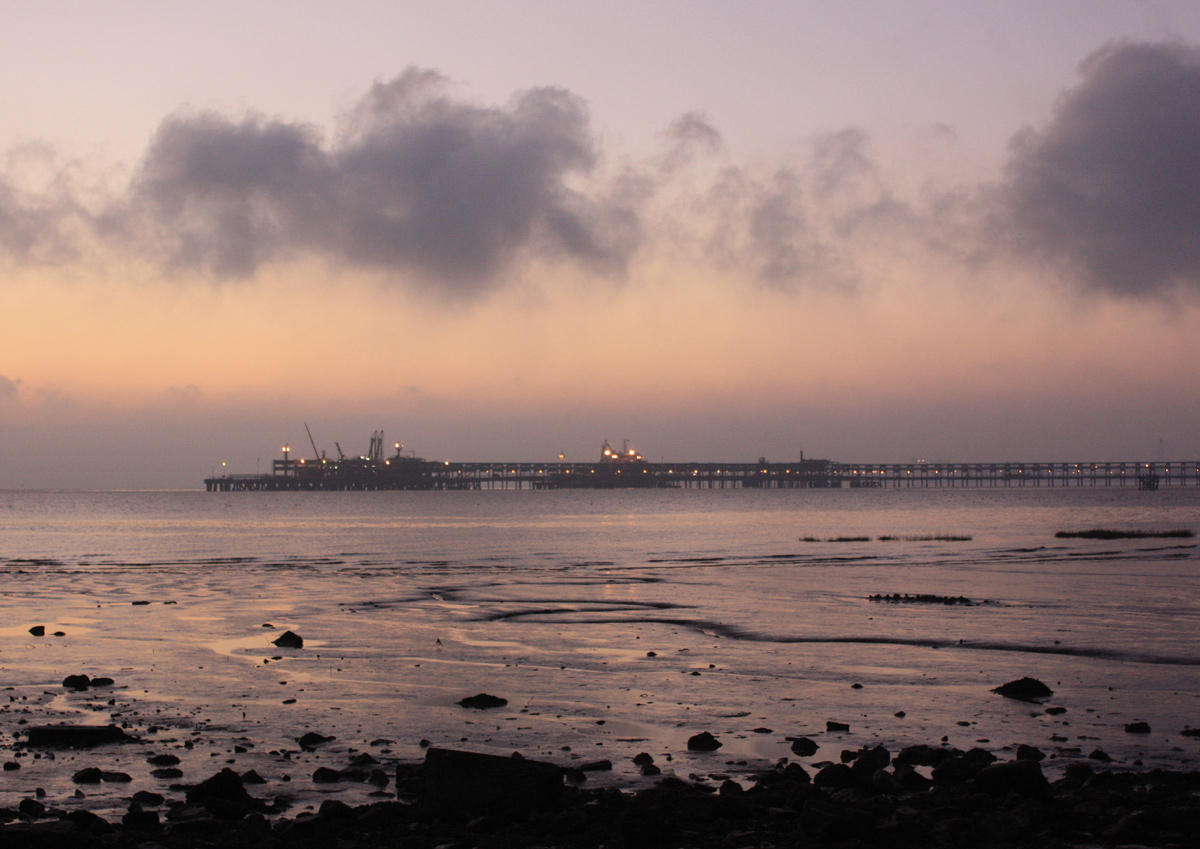
For the duration of the project, collaboration with the ABP jetty master was key, with daily co-ordination of works being essential to the planning, as the availability of the works area would change depending on the shipping schedule and chemical unloading requirements. There were also monthly jetty outages for planned maintenance, which the team needed to accommodate, as well as specific traffic routes to manage for material deliveries and plant.
The use of V-Deck™ provided significant value engineering for the client, and a number of efficiencies on site, meaning the project was completed more than a week ahead of programme, and proved the system is the ideal solution for jetty works, even in the most complex of environments V-Deck™ was a much more versatile and cost-effective solution.