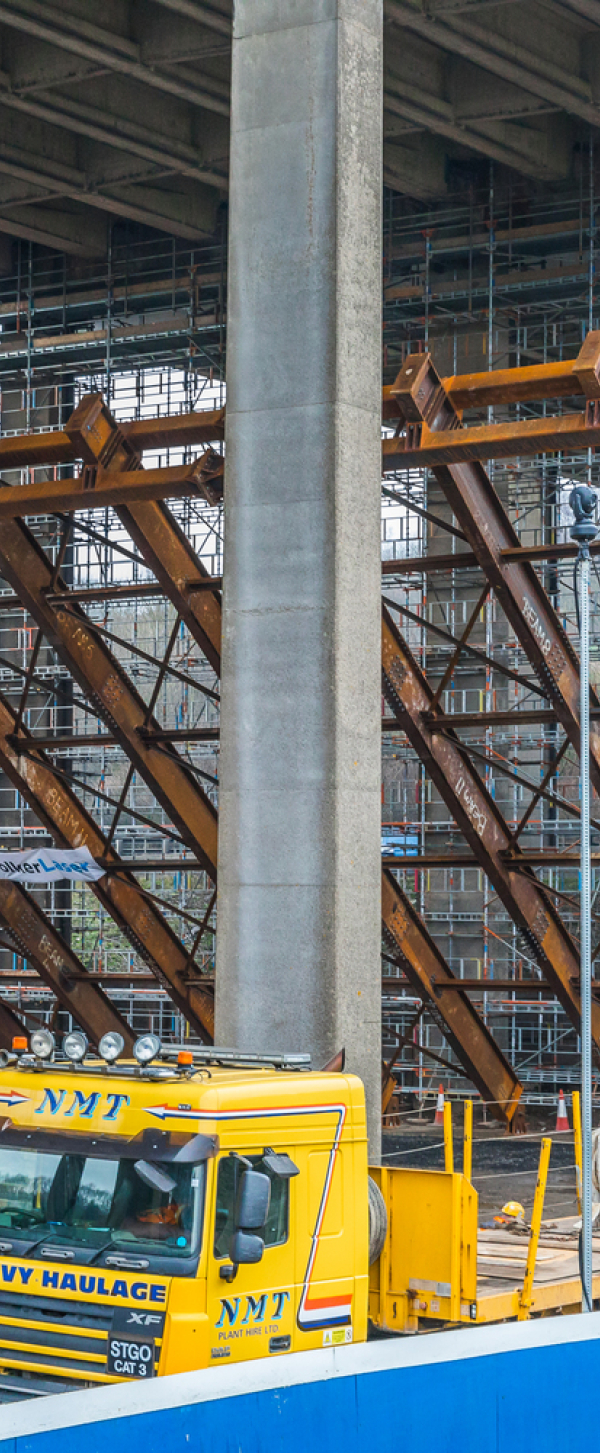
M2 Stockbury Viaduct
Following over six months of Early Contractor Involvement (ECI), VolkerLaser was contracted to undertake bearing replacement works at the M2 Stockbury Viaduct in Kent.
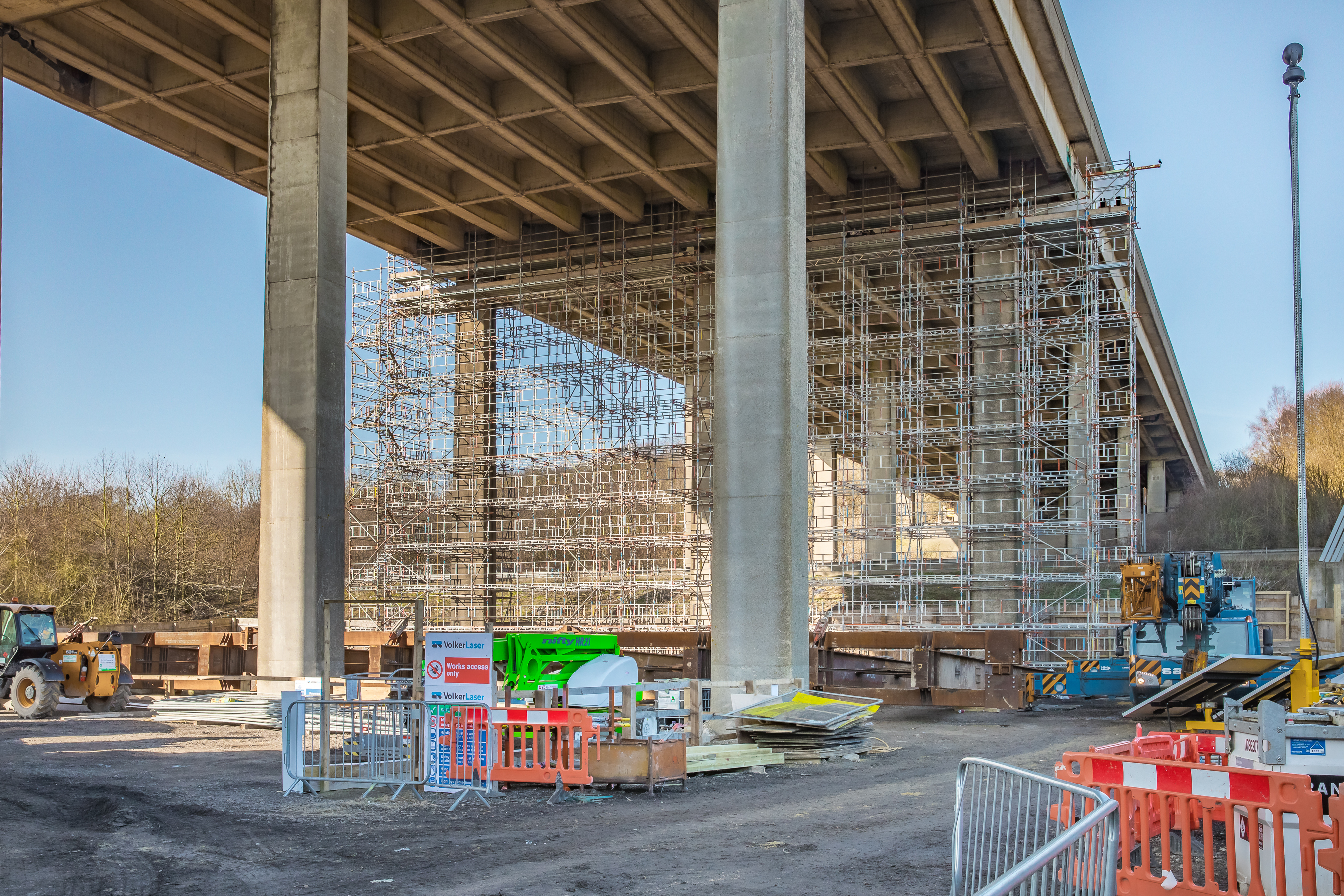
What we did
Forming part of the wider scheme of improvements to the strategic road network from the Port of Dover, vital bridge replacement works were identified on the structure, which was originally built in the late 1960’s.
There were three major elements to the project; the half joint, the east abutment and the west abutment. Each location had 11 rocker/roller bearings which required upgrading with mechanical bearings.
During the ECI phase, our team of experts worked collaboratively with main contractor A-one+ to develop a critical understanding of the structure, designing bespoke temporary works in the form of an 80 tonne steel sway frame for the half joint, and a hanging gallows solution for abutments.
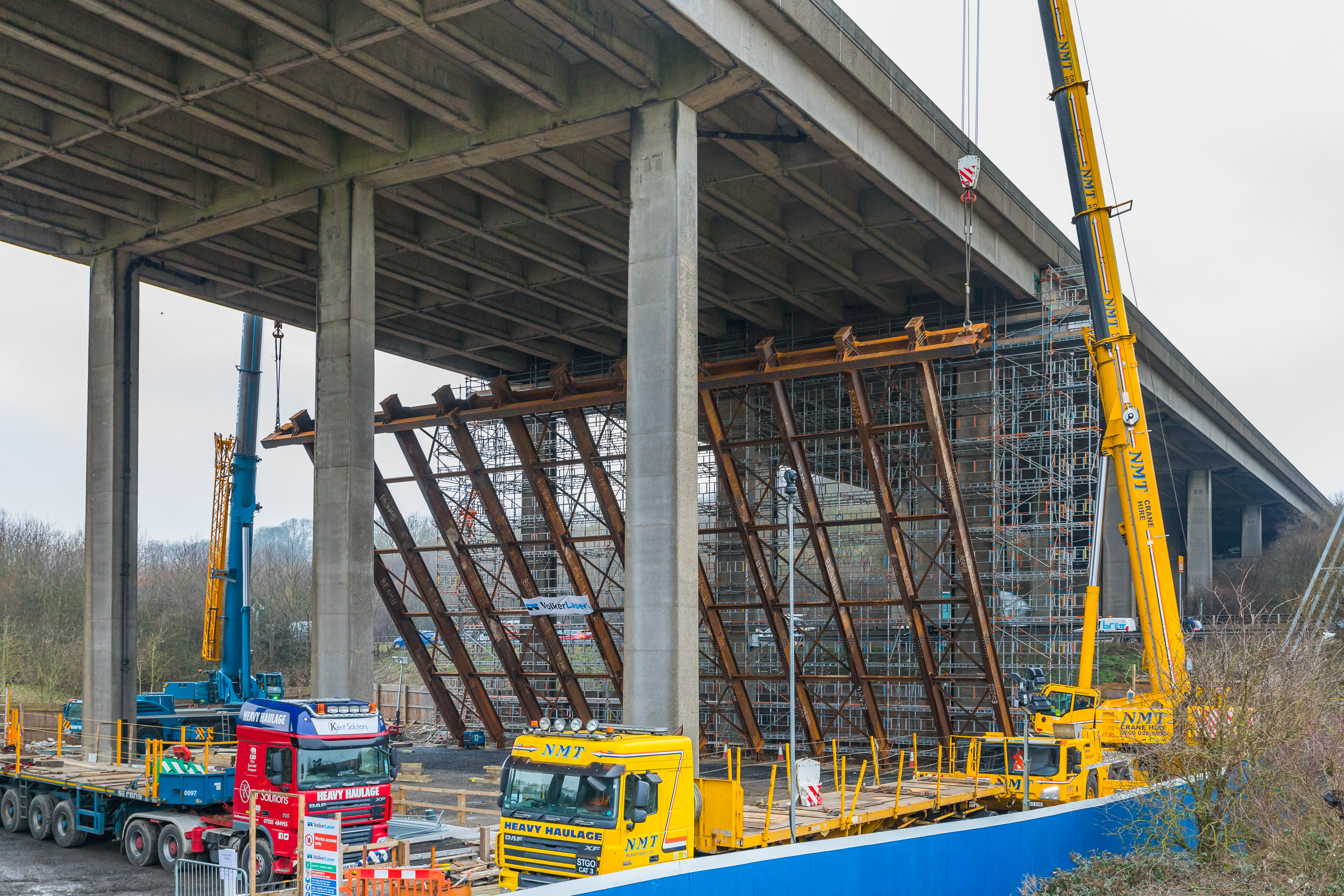
The sway frame required a dedicated pile cap to support the half joint; the pile cap consisted of 22no CFA piles supporting a 34m long concrete pile cap. The frame was constructed at ground level, using 400 steel sections and over 1, 400 tension control bolts and connected to the concrete support beam via a series of hinged joints. The temporary works were lifted into place underneath the half joint by two 250 tonne cranes operating in tandem.
The jacking operation at the half joint was a major exercise in structural expertise, with all 11 beams being jacked simultaneously. Each beam was supported by a 250 tonne jacking assembly, which replicated the bridge articulation and allowed sway. The team commissioned a fully automated 12 point synchronised lifting system to control the jacking.
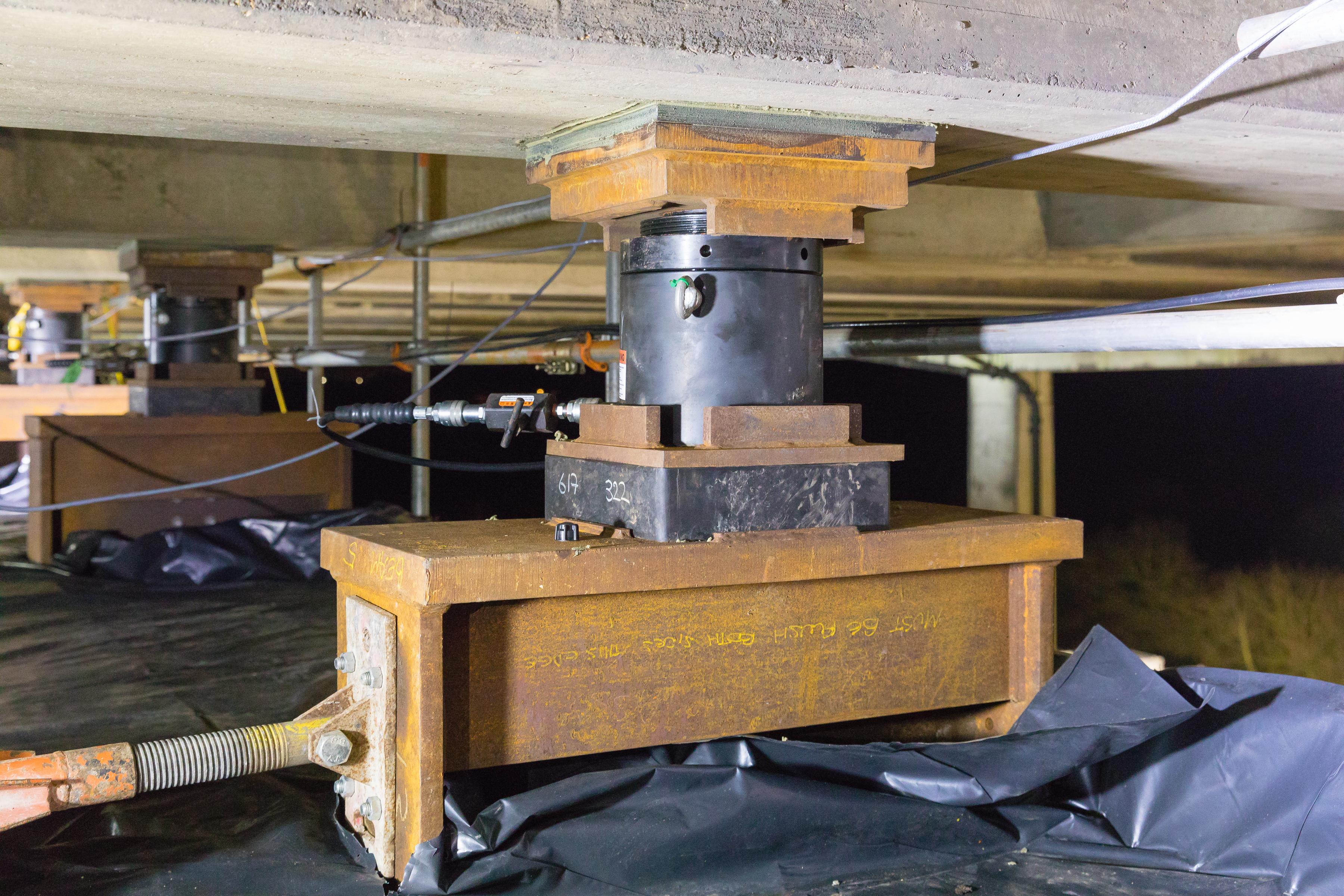
At the abutments an innovative hanger beam solution was required which eliminated speed restrictions and traffic management on the M2, whilst maintaining the bridge fixity. Each beam was jacked individually in four phases, replacing 2-3 bearings per phase. The structural stiffness at the abutments created unforeseen issues which necessitated innovation to overcome, without compromising the replacement operation. The team designed an alternative method of connecting the new bearings to the structure, incorporating a mechanism to preload the bearings.
Undertaking 24-hour shifts where possible, we provided a wide breadth of additional specialist services including, pile testing during ECI, installing CFA piles, expansion joint replacement, bridge deck waterproofing, kerbing, thermic lancing and high pressure water jetting.